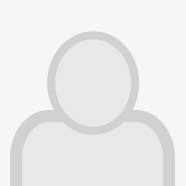
dr hab. inż. Dariusz Fydrych
Employment
- Associate professor at Division Of Structural Materials Technology And Welding
- Dyrektor Instytutu Technologii Maszyn i Materiałów at Faculty Of Mechanical Engineering And Ship Technology
Business contact
- Location
- Al. Zwycięstwa 27, 80-219 Gdańsk
- Phone
- +48 58 348 62 62
- biznes@pg.edu.pl
Social media
Contact
- darfydry@pg.edu.pl
Associate professor
- Division Of Structural Materials Technology And Welding
- Faculty Of Mechanical Engineering And Ship Technology
- Phone
- (58) 348 63 21
Dyrektor Instytutu Technologii Maszyn i Materiałów
- Phone
- (58) 348 63 21
Publication showcase
-
Friction Stir Welding of Aluminum in the Aerospace Industry: The Current Progress and State-of-the-Art Review
The use of the friction stir welding (FSW) process as a relatively new solid-state welding technology in the aerospace industry has pushed forward several developments in different related aspects of this strategic industry. In terms of the FSW process itself, due to the geometric limitations involved in the conventional FSW process, many variants have been required over time to suit the different types of geometries and structures,...
-
Review on friction stir welding of dissimilar magnesium and aluminum alloys: Scientometric analysis and strategies for achieving high-quality joints
Magnesium and aluminum alloys continually attract interest as lightweight structural materials for transport applications. However, joining these dissimilar alloys is very challenging. The main obstacle that hinders progress in dissimilar Mg-Al joining is the formation of brittle intermetallic compounds (IMCs). As a solid-state joining technique, FSW is an excellent candidate to attenuate the deleterious IMC effects in dissimilar...
-
Diffusible hydrogen management in underwater wet self-shielded flux cored arc welding
This article reports the effect of underwater wet welding parameters and conditions on the diffusible hydrogen content in deposited metal for welding with a self-shielded flux cored wire. The diffusible hydrogen content in deposited metal was determined using the glycerin method according to the Plackett-Burman design determining the significance of the effect of the stick out length, welding current, arc voltage, travel speed...
seen 6271 times