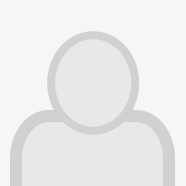
dr inż. Tomasz Seramak
Employment
- Assistant professor at Division Of Manufacturing And Production Engineering
Business contact
- Location
- Al. Zwycięstwa 27, 80-219 Gdańsk
- Phone
- +48 58 348 62 62
- biznes@pg.edu.pl
Social media
Contact
- tseramak@pg.edu.pl
Assistant professor
- Division Of Manufacturing And Production Engineering
- Faculty Of Mechanical Engineering And Ship Technology
- Workplace
-
Centrum Nanotechnologii B Centrum Matematyki
room 209 open in new tab - tseramak@pg.edu.pl
Publication showcase
-
Effects of Micro-Arc Oxidation Process Parameters on Characteristics of Calcium-Phosphate Containing Oxide Layers on the Selective Laser Melted Ti13Zr13Nb Alloy
Titania-based films on selective laser melted Ti13Zr13Nb have been formed by micro-arc oxidation (MAO) at different process parameters (voltage, current, processing time) in order to evaluate the impact of MAO process parameters in calcium and phosphate (Ca + P) containing electrolyte on surface characteristic, early-stage bioactivity, nanomechanical properties, and adhesion between the oxide coatings and substrate. The surface...
-
The Effect of Surface Modification of Ti13Zr13Nb Alloy on Adhesion of Antibiotic and Nanosilver-Loaded Bone Cement Coatings Dedicated for Application as Spacers
Spacers, in terms of instruments used in revision surgery for the local treatment of postoperative infection, are usually made of metal rod covered by antibiotic-loaded bone cement. One of the main limitations of this temporary implant is the debonding effect of metal–bone cement interface, leading to aseptic loosening. Material selection, as well as surface treatment, should be evaluated in order to minimize the risk of fraction...
-
Powder metallurgy of the porous Ti-13Nb-13Zr alloy of different powder grain size
The objective of the present project was to determine the effects of powder granulation (fraction of grain size) for the Ti-13Nb-13Zr alloy, produced by powder metallurgy, on its porosity, grain cohesion, compressive strength, and Young`s modulus. Two powder fractions, 45–105 µm, and 106–250 µm were applied. The 50 mass pct of NH4HCO3 was added as a space holder. The specimens were in compaction stage uniaxially pressed at pressure...
seen 2392 times