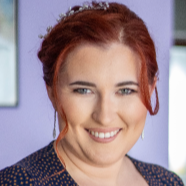
dr inż. Natalia Stawicka-Morawska
Zatrudnienie
- Adiunkt w Instytut Mechaniki i Konstrukcji Maszyn
Obszary badawcze
Media społecznościowe
Kontakt
- natalia.morawska@pg.edu.pl
Adiunkt
- Miejsce pracy
-
Budynek M-T
pokój 112 otwiera się w nowej karcie - Telefon
- +48 58 3471542
- natalia.morawska@pg.edu.pl
Uzyskane stopnie/tytuły naukowe
-
2022-09-21
Nadanie stopnia naukowego
dr inż. inżynieria mechaniczna (Dziedzina nauk inżynieryjno-technicznych)
Wybrane publikacje
-
Adjusting the Stiffness of Supports during Milling of a Large-Size Workpiece Using the Salp Swarm Algorithm
This paper concerns the problem of vibration reduction during milling. For this purpose, it is proposed that the standard supports of the workpiece be replaced with adjustable stiffness supports. This affects the modal parameters of the whole system, i.e., object and its supports, which is essential from the point of view of the relative tool–workpiece vibrations. To reduce the vibration level during milling, it is necessary to...
-
A method of predicting the best conditions for large-size workpiece clamping to reduce vibration in the face milling process
The paper presents an innovative method of solving the problem of vibration suppression during milling of large-size details. It consists in searching for the best conditions for clamping the workpiece based on a rapid modal identification of the dominant natural frequencies only and requires repetitive changes in the tightening torque of the clamping screws. Then, by estimating the minimum work of the cutting forces acting in...
-
An Experimentally Aided Operational Virtual Prototyping to Obtain the Best Spindle Speed during Face Milling of Large-Size Structures
Abstract: The paper presents an original method concerning the problem of vibration reduction in the general case while milling large-size and geometrically complex details with the use of an innovative approach to the selection of spindle speed. A computational model is obtained by applying the so-called operational approach to identify the parameters of the workpiece modal model. Thanks to the experimental modal analysis results,...
wyświetlono 2776 razy